CCM – Continuous Compression Molding for Closures
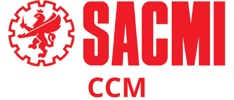
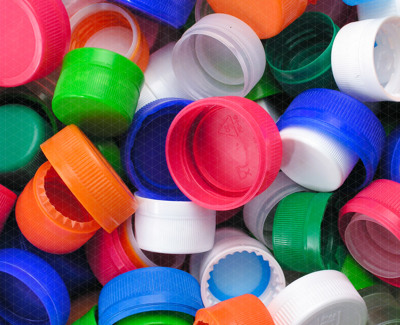
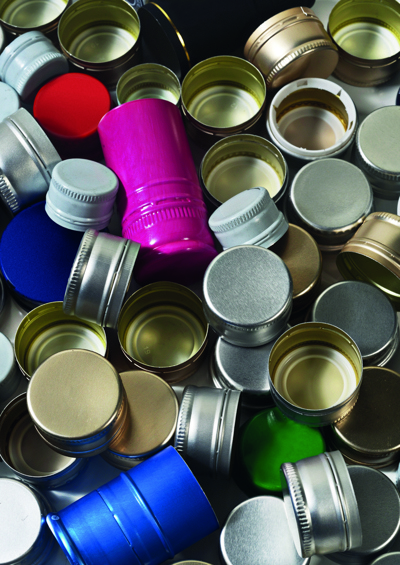
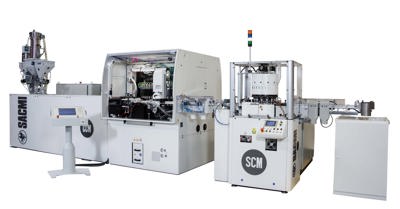
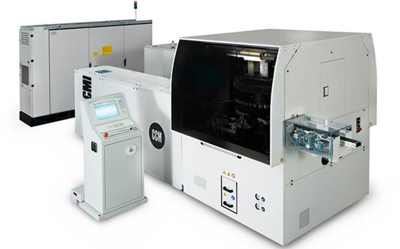
SACMI’S CCM hydraulic rotary presses are specially designed to produce thermoplastic products by means of compression.
HOW IT WORKS:
A continuous work cycle is carried out, during which the plastic material is fed by a plasticization unit, cut into suitably sized pellets and then inserted inside the cavities.
A hydraulic system clamps the moulds at a pressure which can be adjusted even while the production cycle is in progress.
The task of the extruder is to plasticize the compound; that means melting, mixing and preparing the melt correctly for the lining process.
The bulk of the energy needed to plasticize the compound comes from the mechanical friction of the screw-barrel-material system, not the heating elements on the barrel.
MARKET LEADING TECHNOLOGY:
More than 65% of plastic beverage caps are produced through compression and Sacmi is the world-leading compression moulding machine supplier with over 1500 CCM presses installed worldwide.
COMPRESSION MOLDING ADVANTAGES:
- Shorter cycle time & therefore higher productivity
- Less energy consumption
- High specific density
- Maintnance-free moulds that last decades
- Quick colour changeover process
- Less waste = lower costs